Renishaw and Hartford combine to deliver intelligent 'smart factory' solutions
Established in 1965, Hartford is Taiwan's biggest exporter of CNC machining centres as well as being the country's largest machining centre manufacturer.
Developments in Industry 4.0 technology and world shortages in skilled labour have meant that CNC machine manufacturers like Hartford are placing greater emphasis on automation, connectivity, data transparency and ease-of-use. However, achieving Industry 4.0's goals of ‘intelligent manufacturing' and the ‘smart factory' still relies on accurate and effective process control systems.
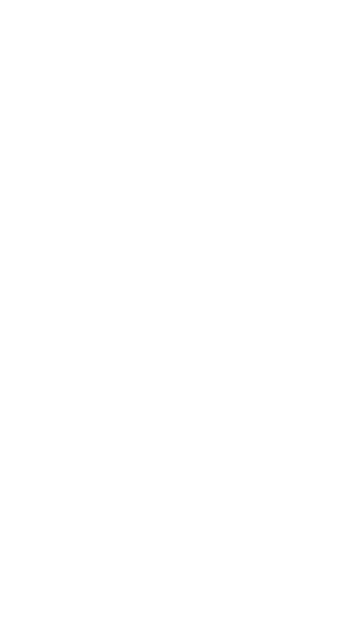
Achieving the goal of ‘intelligent manufacturing'
At its manufacturing facility in Taiwan, the company produces a complete range of medium to large-sized three-axis and five-axis CNC machines for use in major industry sectors including aerospace, automotive, electronics and energy.
Helping customers cope with the widespread shortages of skilled labour presents Hartford with a vital challenge to address. Mr. Bruce Lin, Manager of Hartford's R&D Intelligent Technology Department explained: “Our customers are needing to process work pieces of increasing complexity, however a lack of skilled labour means they are having to insist on machining centres that are even simpler to use.”
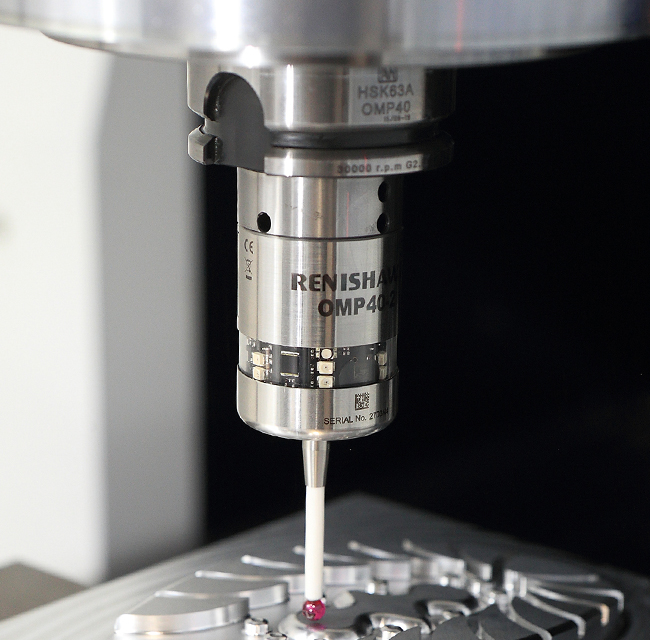
Intelligent HMI with Renishaw app
Hartford developed Hartrol Plus - an intelligent controller as simple to use as a smartphone, integrated into Renishaw's Set and Inspect on-machine app, to make machine tool operation and human-machine interactions simpler and more intuitive.
Operators no longer need to commit machine code instructions to memory, reducing data entry errors and programming times, as well as increasing processing efficiency by as much as 20%.
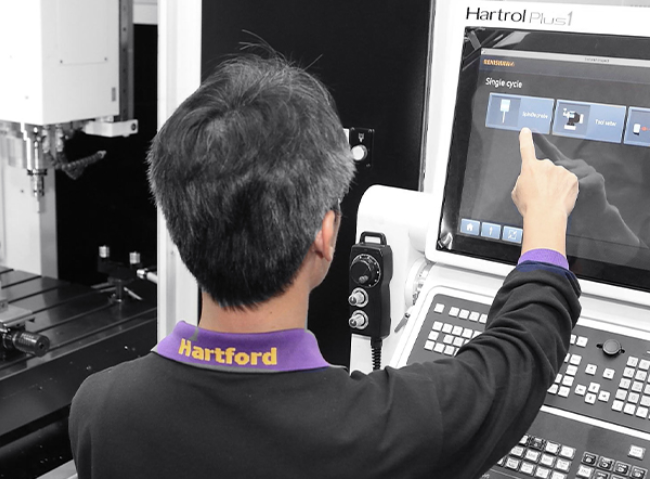
Precision measurement for high quality CNC manufacturing
The precision of all CNC machined components is verified using Renishaw PH20 5-axis probes on coordinate measuring machines (CMMs).
Every Hartford CNC machine not only undergoes 100% laser verification and ballbar testing before dispatch, it can also use the customer's own workpiece for processing verification, with Renishaw OMP40, OMP60, and RMP60 machine tool measurement probes used to measure the precision of the processed work piece.
AxiSet™ Check-Up for rotation centre compensation
Hartford also uses Renishaw AxiSet Check-Up. It provides CNC machine users with a fast and accurate way to check the location of rotary axis pivot points and automatically compensate, if necessary. AxiSet Check-Up does not need to rely on operator experience.
Mr. Lin said, "All machine tools can suffer from wear and drift after a certain period of usage. We therefore recommend that users perform scheduled checks on machine tools using AxiSet Check-Up every 6 to 12 months, in order to ensure that the level of machining precision remains consistent and productivity remains high."
Hartford's imaginative use of leading-edge Renishaw measurement solutions over time has helped sustain its global competitive edge and reflects Hartford's bold corporate philosophy: “We are here to make the best machines to the highest standards.”