Process-controlled hard turning cell pays for itself in 18 days
Conroe Machine is a relatively young company, founded in 2000. While it is a general-purpose shop, Conroe's location near Houston results in a high percentage of business from the oil and gas industry, principally for drilling components. It is doing what most machine shops only dream of – hard turning a family of parts around the clock in an unmanned cell that operates a ‘self controlled' process. It integrates a FANUC robot with the Equator™ gauging system using Renishaw EZ-IO software for 100 percent part inspection. The company states that the turning cell paid for itself in an amazing 18 days.
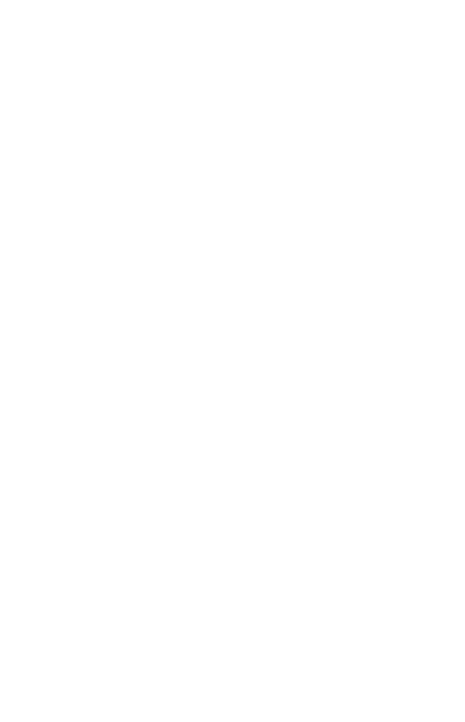
Moving up the automation ladder
"Our production plateaued at 800-1000 parts per day with these two cells, so 400-500 per cell,” explains James Wardell, CNC Programmer. “We had a single operator loading the machines and inspecting the parts. However, you can rely on an operator to correctly inspect only so many parts with this kind of volume, and we needed even more output."
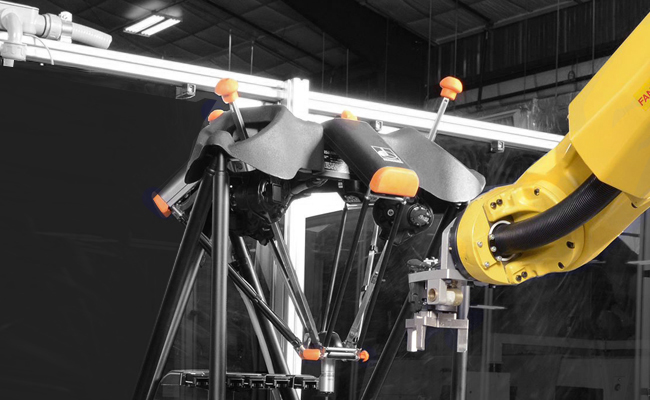
Why Equator™?
“For our next step up, we conceived a fully automated process for the finish machining, with automatic part loading, post-process measurement, automatic tool compensation, part engraving, and boxing/palletising the parts,” he adds. “Inspection must be fast to keep up with the cycle times on the parts, which can be as short as 98 seconds. While working with Renishaw on other projects, the regional manager, Sheila Schermerhorn, introduced us to the Equator™ as a possible solution.”
Process-control tools and software
Equator™ is a low-cost, flexible alternative to dedicated gauging. A master part with known measurements taken on a CMM is used to ‘master' the Equator™, with all subsequent measurements compared to the master.
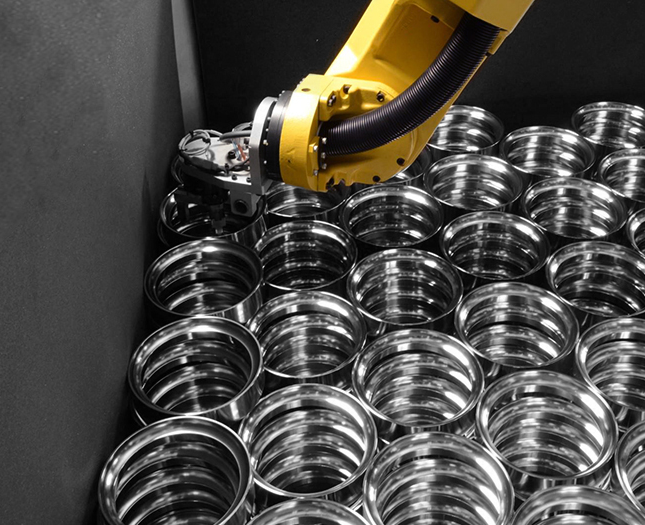
Equator™ in the automated cell
James Wardell and Jeff Buck, Robotics Technician went on to install a cell consisting of the Okuma 2SP-250H, a single Equator™, an engraving machine, and a FANUC M20iA 6-axis robot.
“We developed our own tool compensation software to run on the OSP control,” says Wardell. “This software uses measuring results from the Equator™ to offset the tools when the part deviates from tolerance. The Equator™ is easily able to measure within our tolerances with a high margin.”
Process control
“Our OD/ID stays spot on, with approximately 5 microns variation on radius. We batch parts by size, so changeovers of chuck jaws and other tooling are minimized. The Equator™'s speed allows it to easily keep pace with the process. We re-master only once a day, because our shop is climate controlled to 72 °F” (22.2 °C).”
Inspection principles and automated flexibility
The measuring methodology for the parts is simple. Wardell explains: ‘’We planned the measurement process to work without a part fixture or stylus changing. The robot chooses, through the EZ-IO automation software on the Equator™, which measuring program to run for each type of part. We know the critical features we must measure to ensure the part is within tolerance.”
Measuring/sorting used parts
The hard turning cell currently produces about 600-700 finished parts per day, so only one cell is now needed compared to two before. “For our machining cell, there was no other cost-effective, shop-floor measuring tool comparable to the Equator™,” Wardell adds.
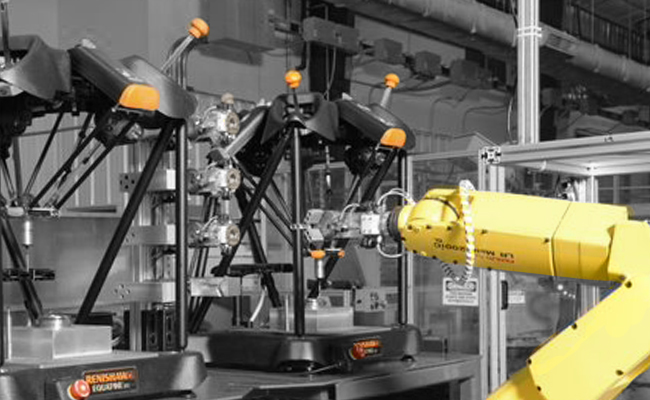