Bastion Cycles takes ownership of its metal AM capabilities
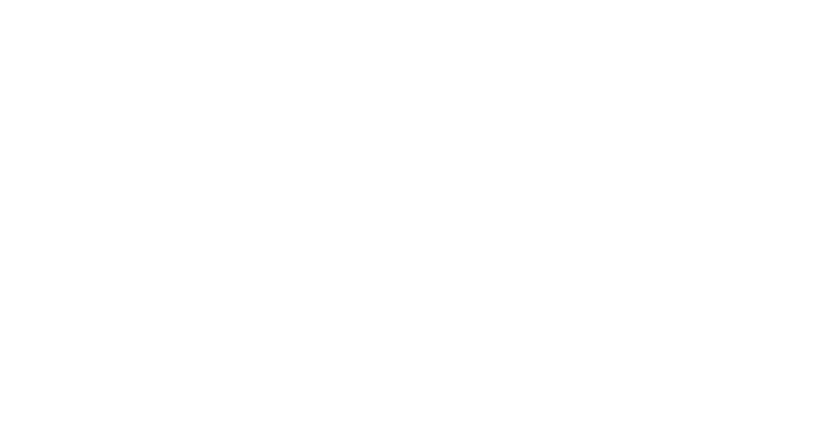
Bastion Cycles, based near Melbourne, Australia, designs, develops, trials and markets high-
performance road bikes made using additively manufactured titanium components. Their frames are
described as "the riders holy grail" and using Bastion Cycles' online bespoke design tool, customers
can design and modify their bike and follow the production process from beginning to end, assured in
the knowledge that their custom-built bike will last a lifetime.
The company transitioned from outsourcing their AM needs by investing in Renishaw's AM250 system
to focus on in-house production. Traditional methods of manufacture such as CNC machining or
moulding do not allow for a lot of flexibility or customisation. In turn, many riders have to compromise
on the size of their bike frame. The adoption of AM opens the door for re-designing and re-
engineering bike frames, optimising strength and functionality and customisation.
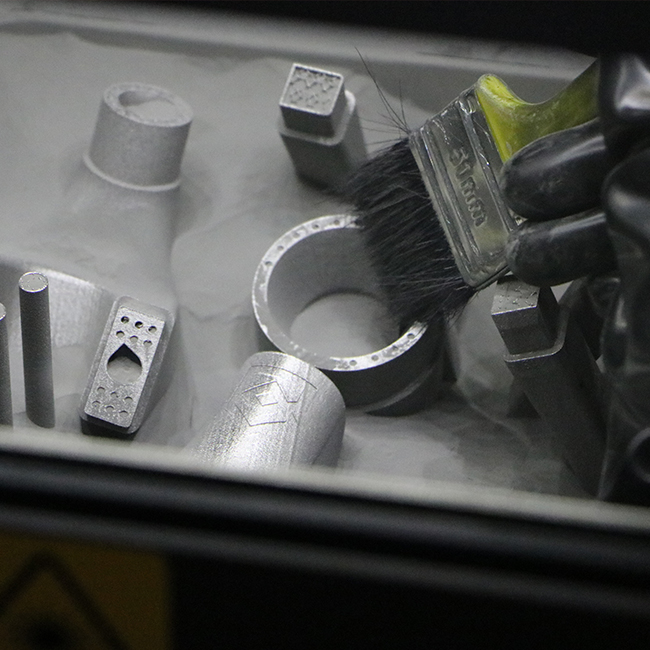
At the end of 2018, with a critical volume of bike sales reached, the decision was made to bring theAM process in-house. Four AM systems from various suppliers were used to trial samples. Renishaw'sAM250 system produced the best surface finish and material performance, together with mass-customisation capabilities and little-to-no inventory required, equating to huge benefits for a smallbusiness starting out on their AM journey.
Bastion's decision to choose Renishaw to supply their AM system, at a critical juncture in the growth of the company, had also been influenced by the level of serviceability of the system and the support available from Renishaw.
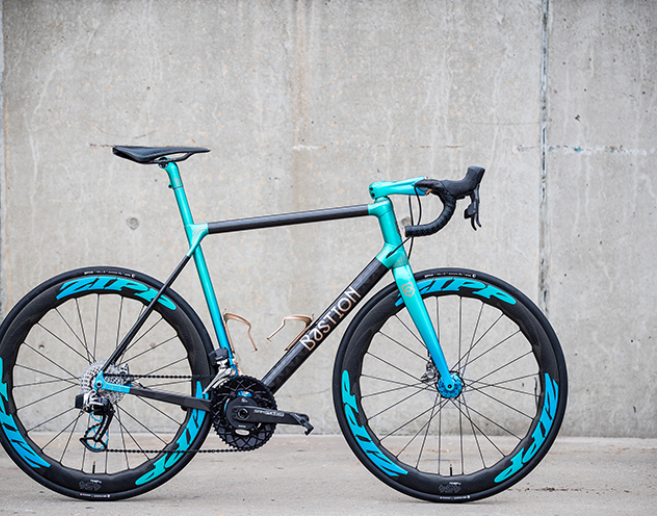
“Australia is a new and, I would say, fairly small AM market. Renishaw is the only AM company that
has committed to have a local headquarters with dedicated staff and a full suite of spare parts,”
remarked Bastion Cycles Co-founder Ben Schultz.
“Additive manufacturing is the secret to the customisation and performance of our bikes and a real
differentiator. Other brands produce lugged titanium with carbon fibre tubing frames, but they all
manufacture the lugs by welding tubes together. We are able to manipulate the shape of our lugs and
add a super lightweight lattice to the inside of them, which means we can achieve exceptionally high
lateral and torsional stiffness, similar to what you find in a carbon fibre monocoque frame and at a
similar weight,” commented Bastion Cycles co-founder, James Woolcock.
AM technology offers new possibilities which cannot be achieved through traditional bike
manufacture methods. The capability to vary the geometry for every single bike frame allows
complete customisation for every customer. AM also provides the ability to produce extremely thin
walls that can vary from 0.25 to 1.5 mm. The internal lattice structure and the aesthetic styling
character lines that add beauty and elegance, all contribute to the creation of Bastion's breakthrough
bike frame design.
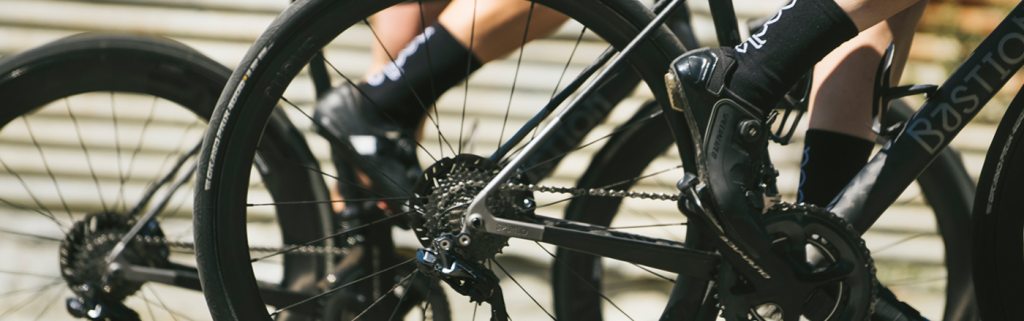